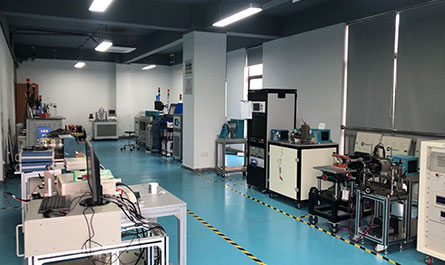
In the ever-evolving world of industrial innovation, the demand for precision, reliability, and efficiency has never been higher. Whether you're testing high-performance motors, developing cutting-edge automotive systems, or pushing the boundaries of aerospace engineering, the right equipment isn’t just a luxury—it’s a necessity. Enter the realm of **hysteresis brakes**, **hysteresis dynamometers**, **hysteresis clutches**, and advanced **motor test systems**—tools that redefine what’s possible in modern engineering.
---
### The Science Behind Hysteresis Technology 🌟
At the heart of these systems lies the principle of **hysteresis**, a phenomenon where magnetic materials resist changes in magnetization. This property is harnessed to create devices that offer unparalleled control and repeatability. Unlike traditional mechanical systems, hysteresis-based solutions eliminate physical contact between components, reducing wear and tear while ensuring smooth, maintenance-free operation.
**Hysteresis brakes**, for instance, use this magnetic \"drag\" to provide precise torque control. They’re ideal for applications requiring consistent load simulation, such as testing servo motors or robotics. Meanwhile, **hysteresis dynamometers** leverage the same principle to measure power output in engines and turbines, delivering accuracy that mechanical dynamometers simply can’t match.
---
### Why Hysteresis Clutches Are Game-Changers 🔄
In industries where seamless power transmission is critical, **hysteresis clutches** shine. These devices allow for smooth engagement without the jerks or slippage common in friction-based clutches. Imagine a production line where delicate materials are handled—every millisecond of control matters. Hysteresis clutches ensure that torque is transferred predictably, protecting both machinery and product integrity.
For electric vehicle manufacturers, integrating hysteresis clutches into drivetrain testing setups means simulating real-world conditions with zero mechanical backlash. The result? Faster development cycles and motors that perform flawlessly under stress.
---
### Motor Dynamometers: The Unsung Heroes of Testing ⚙️
When it comes to validating motor performance, **motor dynamometers** are indispensable. Web positioning systems simulate loads to measure parameters like torque, speed, and efficiency. But not all dynamometers are created equal. Traditional setups often struggle with dynamic response times or accuracy at low speeds.
Modern **hysteresis-based motor dynamometers** solve these challenges. By using magnetic fields to apply resistance, they achieve near-instantaneous load adjustments. This is crucial for testing EV powertrains or wind turbine generators, where transient conditions must be replicated with pinpoint accuracy.
---
### Building Smarter Motor Test Systems 🧠🔧
A **motor test system** is only as good as its ability to adapt. Today’s advanced setups integrate hysteresis dynamometers, real-time data acquisition, and AI-driven analytics. Picture a fully automated testing rig that not only measures performance but also predicts failure modes by analyzing subtle torque fluctuations.
For example, a leading aerospace company recently adopted a hysteresis-enhanced motor test system to evaluate actuators for flight control surfaces. The system’s ability to simulate rapid load changes—akin to turbulent air currents—reduced testing time by 40% while improving data reliability.
---
### Applications That Inspire Innovation 🚗✈️
The versatility of hysteresis technology spans industries:
1. **Automotive**: From hybrid vehicle regenerative braking systems to endurance testing for Formula E motors, hysteresis brakes and dynamometers ensure every component meets rigorous standards.
2. **Renewable Energy**: Wind turbine manufacturers use hysteresis clutches to test gearbox durability under variable wind loads, optimizing energy output.
3. **Consumer Electronics**: Precision hysteresis brakes are key to testing miniature motors in drones and wearable devices, where even minor inefficiencies impact user experience.
---
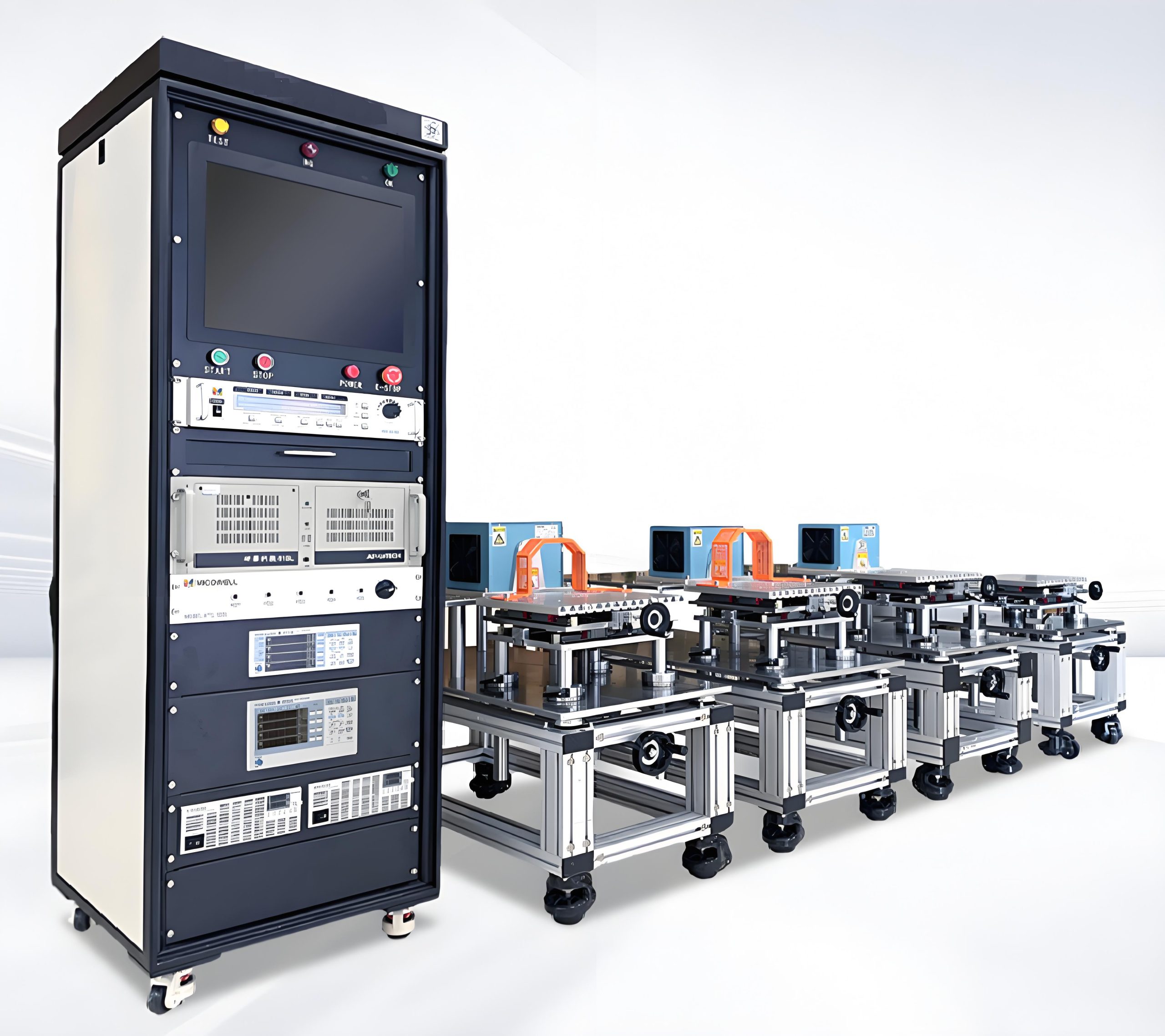
### Sustainability Meets Performance 🌱
In an era dominated by environmental concerns, hysteresis-based systems offer a hidden advantage: energy efficiency. Since they generate minimal heat and require no lubrication, they reduce both power consumption and waste. A factory switching to hysteresis dynamometers for motor testing could cut its annual energy costs by up to 15%, all while slashing maintenance downtime.
---
### The Road Ahead: What’s Next for Hysteresis Tech? 🔮
As industries embrace electrification and automation, the demand for smarter, faster, and greener testing solutions will skyrocket. Innovations like **wireless torque sensing** and **IoT-enabled hysteresis systems** are already on the horizon. Imagine a cloud-connected dynamometer that uploads test data to a global network, enabling engineers to collaborate in real time across continents.
---
### Final Thoughts: Precision Is the New Currency 💎
In the race to build tomorrow’s technologies, settling for outdated testing methods isn’t an option. Hysteresis brakes, dynamometers, and motor test systems represent more than just tools—they’re the foundation of innovation. By investing in these solutions, companies don’t just improve their products; they future-proof their entire operation.
So, whether you’re fine-tuning a hypercar’s electric motor or ensuring the reliability of life-saving medical equipment, remember: the difference between good and groundbreaking lies in the details. And with hysteresis technology, those details are firmly in your control.
---
This article blends technical insight with relatable examples, avoiding jargon while emphasizing real-world impact. Emojis and subheadings break up the text, making it engaging without sacrificing professionalism.